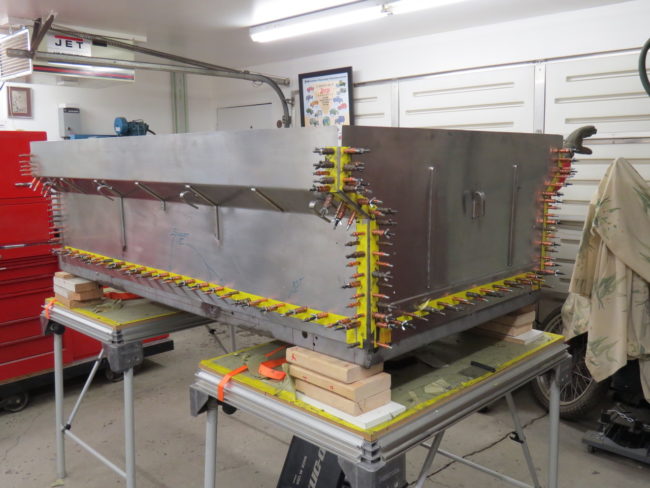
Paul’s made a little more progress on the trailer.
As you might have heard, Alaska was hit with a good-sized earth quake near Anchorage a couple days ago. Our own Anchorage-based Alaska Paul filed this report:
“This past Monday (Nov 26, 2018) my friend First Larry came over to the house and helped me shoot the 90 remaining rivets in the M100 trailer floor section so I could attach the side panels to the floor flange. The seams where these parts overlap is sealed with a two part rubber like sealant and cleco fasteners hold everything together while the sealant hardens.
Usually the sealant cures within 3 or 4 days so this morning (Nov 30, 2018) I was working in the garage cleaning up the excess sealant by 8am. Because the trailer is sitting on two work tables it’s necessary for me to stand on a 5 gallon bucket which allows me to bend at my waist to clear the trailer sides while still being able to reach the floor panel.
This was the position I was in when Mother Nature decided to remind me just who was really in charge of my life.
We got hit with a sharp jolt and then the garage began dancing. As I was holding onto the trailer rear panel trying to remain upright I noticed the walls of the garage were flexing hard enough to open and close the walk in door and this door had been latched. For some reason the movement of this door fascinated me so I continued watching (while tightly holding onto the trailer) until I realized the door was opening and closing so fast it looked like it was waving goodbye. I agreed it was a good time to say goodbye to the dancing garage so I bounced my way out of the garage and staggered towards the house.
Unlocking the door to the house took longer than usual since my actions resembled a drunk opening a door while on a ship in a storm. A couple of years ago I’d installed outside grab handles on either side off the kitchen door so I hung onto a handle with one hand while I tried to get the key in the lock with my other hand. I gripped the handle so tight I think I left fingerprints pressed into the metal.
After getting the door unlocked I quickly checked on the Goddess (she was fine) and Samson the wonder parrot who was not amused to have his perch catapult him skyward. Samson sought safety on top of his cage in the living room but the many aftershocks continue to irritate him.
In the brief time it’s taken me to write this email we’ve had six noticeable aftershocks along with many little tremors.
While I’ve been thru stronger earthquakes than the ones we had today this main one was impressive. There are reports of power lines down, sections of local roads destroyed, broken water pipes in commercial buildings and traffic signals no longer operational.
The Goddess and I have been real lucky… we never lost electricity, we still have heat, we have enough food to last for more than 3 weeks and since we’re retired we don’t have to go anywhere. We’ll be staying home where we can help the neighbors if need be.
Oh yeah.
The garage made it thru the quake with no damage to speak of, the little blue house shook and shimmied but it’s fine. Some stuff got broken, some stuff got tossed around but the little Willys and the M100 trailer are both fine.
We’re pretty happy
I’ll send a few photos to show the ground cracking in the back yard (See below).
That’s all,
Paul
The Goddess
and Samson the sleeping Wonder Parrot
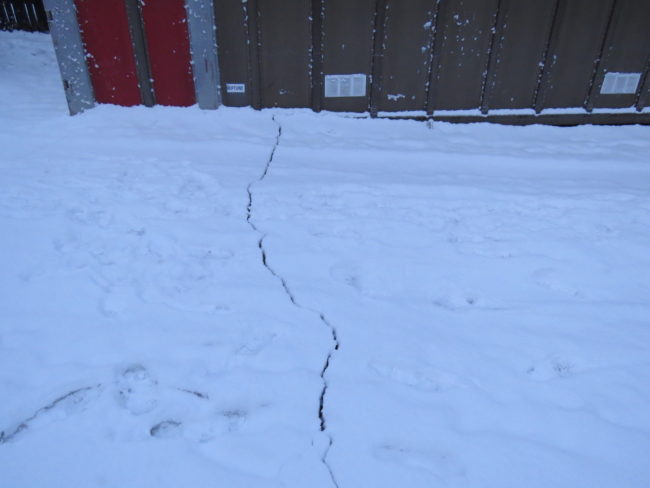