Javier rebuilt this nice looking M-38, thanks it part to finding parts through eWillys and readers comments. During the rebuild, he added a few additional safety features such as Herm’s dual reservoir setup. He notes that M-38 does have a few CJ parts on it as well. The unique frame for the winch was something he and a friend built after testing out different scenarios with cardboard. The winch cover is a nice touch, too. Thanks for sharing Javier!
Builds Research Archives
1949 Directions For Building Toy Willys Wagon
On August 04, 1949, the Wolcott Beacon out of Wolcott, Indiana, published directions on how to build a toy Willys Wagon for kids. The length of this toy is about 7″.
Headlight Bezels Over the Years
The other day someone asked me about headlight bezels (or if you prefer, headlight ‘heads’) and how they changed through the years. I did not have a good answer to that reader’s question, so this working thread about bezels is the result. Along the way, I learned that some folks call these parts “heads”, but perhaps that is more military related?
1. 1945-1946 Early Painted Bezels on CJ-2As
Early CJ-2A bezels were painted, not chromed, until approximately #38687, according to the CJ-2A page. As far as my research indicates, only Walcks carries new, unpainted bezels. This is the flatter style of bezel without the tab.
2. 1946-1953 Later CJ-2As, CJ-3As and 1956-1959 DJ-3As
After roughly CJ-2A #38687 the bezels were chromed, but their shape was the same. They lasted through the end of the CJ-3A production run and into the early DJ-3A production run (1956-1959). These example images are from Kaiser Willys.
3. 1950-1952 M-38s, 1953-1971 M-38A1s, and M-170s:
I didn’t realize that M-38 and M-38A1 bezels were the same. It’s on the M-38a1 site that I encountered the alternative term “head” for the bezel. Peter Debella has NOS rings.
4. 1950 USMC CJ-V35 Blackout Lights ‘bezels’
Thanks to Mike Wixom for helping me out with these rare blackout lights.
This type of headlight bezel, or more correctly blackout ring (although not that effective), was used only on Marine Corps Radio Jeeps as far as I know. Specifically on the CJV35/U and possibly on the MZ-2 and MZ-3 Radio Jeeps from Late WW2. They were installed at the factory on all 1000 CJV35/U Jeeps built in May of 1950. These were eventually replaced by the actual blackout lights found on the M-38.
Because these aren’t readily available, someone posted this writeup on how to inexpensively recreate them:
Here is a different, larger version of a CJ-V35 bezel. Mike believes the ones shown below may have been fabricated and not original, but perhaps the owner can offer input on this.
A Slat Grille Rebuild
There was some debate on G503 back in 2016 about whether a modified jeep for sale was a slat grille MB or not. After seeing the jeep for sale in October of 2016 on eWillys, Kees took a chance that it was a slat grille and bought it.
He had it shipped to Rotterdam, only to learn it was in worse shape than he’d hoped. What happened next was several years of hard work to bring it back into drivable condition. Here’s his story:
Hi Jeepers,
In October 2016, I bought a Jeep that I saw for sale on Ewillys. I had hoped it the Slat Grille I had been seeking, but was it really a Slat Grille?? A lot of folks on G503 were not convinced. Nonetheless, I took the risk.
When it arrived in Rotterdam I was shocked. It was in VERY bad shape. The body was covered in a layer of bondo, up to one inch in places. The sidepanels were almost gone. The gas tank was a drum bolted onto the cargo bed and the body was bolted to the frame with pieces of scrapmetal. There was a giant dent in the dashboard and the front of the jeep was a mess, replaced by bubba modifications. No effort had been made to clean the jeep, so it was covered with rust and dirt.
Did I feel lucky? Not at all. But, it’s not like I could send it back! So, I started forward, one step at a time.
The first thing I did was bring it to our version of the DMV for inspection. The VIN in the title was 11358, but we could not find it on the frame. Fortunately, we did find a body number of 15160. With those two ID numbers the department did some investigation with their American collegues and found out the VIN is 111358. That was great, because they were able to determine that it was an original Slat.
Once that was settled, I sent a lot of detailed photos to an friend who is an expert on Slats. It was from him I learned I had a lot of rare Slat details like axles, body, frame and some engine parts.
The first year was no fun at all. None. Zip. Nada.
I spent month after month cleaning, sandblasting and torching bondo. Yet, under all that bondo, I found perfectly good, shiny metal in some places.
When the body was clean I brought it to a welding expert, a pensionado who liked to keep busy welding. Thankfully, he was not expensive because it took him many weeks to reshape the complete body. The only replacement he did where the 2 side panels and the fuel tank container. He was able to restore all the other parts. In the meantime I was busy cleaning the frame. Continue reading
Flattening a Mitsubishi Fender
Gary shared this Instagram post by catskill_mtn_customs that demonstrates how to alter a Mitsubishi fender into a CJ-3B style fender.
Hudson Steering Modification Pics
Barry Ogletree has been working on another great project, this time has installed a Hudson Steering system on a Willys frame. I’ve seen several jeeps for sale with this system over the years, but I’d never seen the parts up close. According to Barry:
I have found a unique steering conversion on the chassis of the wooden bodied Willys (Woody) that is worth a look. I have tracked down that it is a Hudson Car box. The beauty is that it sits about perfect in the Willys frame rail. 3 bolts and you are done, and it tucks perfectly against the frame for exhaust/pitman arm clearance. This is the best fit that I have seen in years of this kind of work. Regards Barry Ogletree.
Barry was awesome enough to post a bunch of pics at this location: https://texasflatfenders.smugmug.com/STEERING-BOX-HUDSON/
The Swiss Knife of CJ-5s
UPDATE: Back in 2012 I ran across a pic of this CJ-5 on Flickr (1st one shown below). Now, thanks to rob, we have a series of photos of this North Carolina CJ-5, custom built by the owner. Sure looks handy!
Paul Finished His Stainless M-100 Trailer
As always, Paul’s detailed work has resulted in a work-of-art. Well done Paul!
Paul writes, “The earth has calmed down these last few months so I’ve made good progress on the M100 trailer rebuild. In fact, other than measuring the length necessary for the trailer safety chains and the electrical harness everything else is finished. While I still spent over 300 hours to build the stainless steel box and rebuild everything I planned on reusing it was easier than I’d anticipated. I had no idea I’d need so many 2X4’s but the local Home Depot store was happy to take my money.
This photo shows the jig I made to keep the trailer box in alignment while I fabricated the upper tube reinforcement and rolled the sheet metal before tack welding the edges.”
The upper tube has been fitted and held in place with strips of plywood and 24 6 inch C clamps.
I used a plastic hammer to gently form the sheet metal over the curve of the reinforcing tubing. The C clamps were repositioned often to allow hammer access to the 20 feet of 18 gauge stainless sheet metal around the upper edge of the trailer box.
The tack welds are complete so the 2X4 jig can be removed
The replacement box is bolted to the original trailer frame and tie down straps hold the frame to the work tables. I had to plan my work around earthquakes.
Carl Jantz’s Super Jeep
This article, titled SUPER JEEP: A 1942 WILLYS THAT CAN’T BE KILLED, ran a couple years ago on driving line.com, but is still an interesting look at a unique build.
https://www.drivingline.com/articles/super-jeep-a-1942-willys-that-cant-be-killed/
Terry’s CJ-3B
Terry bought this running late model CJ-3B for a great price, then doubled his investment in the jeep by fixing it up and adding some fun extras like rear duallies, a hardtop, and rope (just for kicks). Despite the additions, almost none of it altered the original jeep he bought. He says the changes made the jeep popular with folks and 99% of people didn’t realize it was not a military jeep.
The other day he went into a dealership and the dealer offered to buy it. Though not planning to sell the jeep, the amount offered by the dealer, double Terry’s entire investment in the jeep, was too good to refuse, so he sold the jeep. With his new found cash, he picked up a wagon that he plans to restore. Here are a few pics of the CJ-3B.
Before his changes:
Dave’s 1948 Dually CJ-2A
Dave just scored a Dually adapter kit off of eBay. He’s also got a set of fenders. I really like those Free-Lock hubs, too.
GPW/Truck From Indonesia
Rahadian Dhian of Badung, Indonesia, shared on Facebook this custom jeep made from a GPW and a 1950’s Truck. The top really finishes it off nicely.
1947 CJ-2A Rebuild in Minnesota
This article in the Chanhassen Villager, out of Minnesota, highlights Steve Knigge’s rebuild of a 1947 CJ-2A.
Knardly Rolls Sees the Light of Day
Paul ceremonially rolled Knardly Rolls out of the garage on Monday.
He writes, “Today (May 7th) I opened the garage door and then removed two of the four insulated panels positioned against the outer surface of the garage door so there would be enough room to move the little Willys from the dark garage and into the May sunshine. I quickly learned I need sun glasses. Most of the body has a brushed pattern on the stainless steel but even brushed stainless is rather reflective when the sun is shining. I’m real glad I didn’t polish the body, that would have been blinding on a sunny day.
The little Willys has been moved into the connex where I’ll fuel it up, check for leaks and see if the engine will start. Once the engine runs well I’ll support the Willys with jack stands and begin testing the operation of the transmission and axles.
However, before I begin any ground running I’m going to repaint the interior of the garage. The last time I painted the garage was 30 years ago so new paint is long overdue.
Anyway, here’s a photo of the little Willys escaping from the garage. It was a whole different perspective for me since the small garage only allowed me close up views but once it was outdoors I was able to back away and get a view of the entire Jeep. Quite different from what I’m used to.
I’m still having a hard time believing the little Willys is finally done but seeing it outdoors makes it seem more real.”
Matt’s Rebuilt CJ-3A at Kaiser Willys
Matt shared a feature story about his rebuild of a 1952 CJ-3A. Looks great!
http://blog.kaiserwillys.com/the-restoration-of-ruby-the-1952-willys-cj-3a
Knardly Rolls Rolls for Reals, 32 Years Later ….
Well, he did it. A big CONGRATULATIONS TO ALASKA Paul. He installed the final part onto his stainless 1952 M-38 Knardly Rolls on May 2nd, 2018. I, for one, look forward to hearing about the inaugural run!
To this 32 years and 5 months later:
Here’s what Paul wrote,
“Somehow, despite my best efforts, I finally managed to complete the never ending rebuild of the little stainless steel Willys. The last part (the rear driveshaft) was bolted to the axle at 12:30 pm today, May 2nd 2018 ending a multi decade effort that began when I dropped the engine off at the rebuilders on December 2nd 1985. Over the years I’ve used the date the stainless steel body was ordered as the project start date but that happened over a month after the engine went to the rebuilders.
From the starting date to the completion date this project took 32 years and 5 months of time. I realize I’m slow but I never expected I’d take over three decades to rebuild one Willys Jeep …… it’s good I don’t do this for a living. I’m glad I finished it while I’m still flexible enough to climb into the driver’s seat, the Goddess suggested I make a stainless steel walker because I might need one before I finished the little Willys. She’s helpful that way.
The backyard is quite soggy so I’ll have to wait a week or so before I can reposition the Willys from the garage to the connex for leak checks and static runs. If things go well I hope to be cruising thru the neighborhood by late May.
Naturally, the garage must be filled with a project before winter so this fall I’ll move the remains of the 1951 M100 trailer inside where I’ll begin to fabricate a stainless steel box on the original frame.
Other than that the Goddess and I are having fun under the midnight sun here in the northland. By mid May the trees should have leaves, the night time temperature should stay above freezing and we shouldn’t have anymore snowfall until late September.”
Danny’s Junk to Jewel Jeep
Danny recently finished the restoration of his jeep (MB?). It only took him two years (“that’s 2 years of hard graft,” he wrote). A recent, unusual storm, in the United Kingdom gave him a chance to snow-test it. Looks like he had fun!
After:
Nate’s Hydraulic Assist For His CJ-3A
Nate’s at it again. He got to thinking about upgrading his steering on Ted, his CJ-3A. One thing led to another and soon he was developing a fairly non-invasive (no saginaw-like alterations) way of improving his steering. He’s spent the past month and a half writing it up on the earlyCJ-5 page.
http://www.earlycj5.com/xf_cj5/index.php?threads/teds-steering-upgrade-with-a-twist.128518/
Here are a few pics.
Maury’s New Batter Topper
Maury share how he tackled making his new-style battery look old school. you can follow the thread at earlyCJ5.com.
http://www.earlycj5.com/xf_cj5/index.php?threads/new-battery-topper.128802/
More From Paul
Paul shared a couple of other recent milestones on his Willys journey.
1. The Throttle Spring:
After hooking up the throttle linkage to the carb (a cable system) I realized not only was I missing a throttle return spring but I was also missing a throttle return spring attach point. A trip to the local auto parts store provided me with a selection of different throttle return springs but I was on my own when it came to the spring attach point. More poster paper was sacrificed to make three patterns before I came up with a return spring attach bracket I liked and that would fit without getting in the way of the distributer cap. I made the return spring attach bracket from stainless steel and incorporated a fastener to allow a coil wire clamp to be bolted to the bracket.
Here’s the cable throttle linkage, the throttle return spring, the return spring attach bracket and the clamp for the coil wires. The red on the return spring is dried blood …. I managed to poke myself quite a few times while attempting to curl the spring ends to match the attach brackets and those springs are sharp. Oh well, some folks pay people to poke them with needles and call it acupuncture. All I have to do is go out to the garage and work on the little Willys, there’s always some sharp edged stainless part waiting to cut me before I even realize it. That metal can be mean sometimes.
2. The Front Drive Shaft:
The position of the V6 engine made the original front driveshaft too long and the rear driveshaft too short but right now I’m concentrating on the front driveshaft only. I bead blasted the front driveshaft, took the necessary measurements between the transfer case outlet and the front axle attach point and it was time to visit with the local driveshaft guys. After cutting the driveshaft to the correct length it was welded back together, new universal joints installed and then balanced before returning to me. I removed the new u joints, did a quick bead blast cleanup (after removing all traces of the really sticky grease on the splines) and dropped it off to have it powder coated.
The next day the driveshaft was ready to come home so I could reinstall the new universal joints and then bolt this thing on the little Willys. The last time this driveshaft was installed on the little Willys was when it did it’s major meltdown in October of 1985. Wow, I’ve been waiting over 32 years to reinstall this driveshaft. It doesn’t seem it’s been that long but the color (or lack of it) or my hair tells me more than a few decades have gone by. I remember when I was still in my 30’s my hair was brown, not Arctic Blonde (White) like it is now.
Oh well, as much as I tried to take my time installing the driveshaft the four u bolts were quickly tightened and torqued and it was time to find the next to do item on the little Willys.
The front driveshaft is installed on the little Willys for the first time in over 32 years. WOW!
Paul’s Deflecting the Heat
Paul shared this update on some custom heat shields for Knardly Rolls.
Paul writes, “The exhaust manifold is closer to the steering linkage than I’d originally intended but there isn’t any easy way to increase the distance between these two systems so I decided the best solution to this problem was to make some stainless steel heat shields that would bolt to the fender and fit between the exhaust manifold and the steering linkage.
First I quickly made a test shield from some leftover poster board so I could check how this paper part would fit before I cut any stainless sheet. Once I had the shape of the heat shield figured out I made a test piece from thin gauge aluminum.”
“First I made a test heat shield from poster board to check for the correct shape. Once I was satisfied with the shape of the heat shield I made one from thin aluminum to double check any clearance issues. After the aluminum shield was modified I made a third shield from thin stainless sheet but I saw a need to fit the fourth and final heat shield a little closer to the manifold and also use a thicker gauge of stainless to prevent unwanted flexing during use. Once the fourth shield was fitted I drilled the attach holes and bolted the shield to the front fender.”
“Here’s the final heat shield temporarily attached to the front fender using Clecos so I could drill the fender and the heat shield at the same time.”
“As you can see, the double U joint between the lower end of the steering column and the first steering shaft is still exposed to heat from the exhaust manifold so another heat shield was necessary. This smaller heat shield will be attached to the steering column by adel clamps so it’s easily removed for maintenance. The two adel clamps are bolted to the column with enough threads exposed on the fasteners to attach the aft end of the second heat shield while the forward end of the second shield attaches to the aft end of the first heat shield where the two empty holes can be seen. If you read that last sentence fast it sounds like a square dance call.”
“Here’s the paper pattern and the finished stainless steel second heat shield ready for installation.”
“With the second heat shield installed I think most of the exhaust manifold heat will be deflected away from the steering linkage thus preventing damage to the U joints and shafts.”
“An underside view shows the clearance between the steering linkage and the heat shields”
Alaska Paul’s Placard Progress
Today’s the last day of the year, so let’s go out in style with Alaska Paul’s placard progress. Paul understands that his one-of-a-kind electrically and mechanically designed jeep will require information assistance just in case any of us lesser mortals attempt to drive it. So, he spend some time over the holidays playing with placards.
Paul writes, “It’s been a while, so I figured I’d send some Willys progress photos your way. This photo is of the fuel valves between the front seats with an engraved placard sitting on the metal cover. A local sign shop (Alaska Laminated Signs) made up some test placards so I could see how different colors would look with the stainless, gray and blue interior of the Willys. While this placard has all the necessary information and the correct shape to fit the metal cover plate I wasn’t too happy with the black background and the white lettering. I wanted something with more visual appeal so Dave (the sign shop owner) duplicated this placard using a brushed aluminum outer layer over a black base.(see next pic)”
“This aluminum/black combination looks good by itself but I didn’t feel it looked good when it was placed next to the stainless steel parts so Dave made a third placard using a dark blue upper layer and a white base (see next pic).”
“Now this is what I was looking for. While the blue on the placard isn’t a perfect match to the blue on the seats they’re close enough so they look good together and the contrast between the white letters and the blue background makes it bright and easy to see. Now that we had a color selected I gave Dave my metal full size patterns for the five placards needed for the little Willys and he began the cutting and engraving process.”
“Here’s the finished product. From left to right we have the overhead switch placard, the circuit breaker placard and below that is the fuel tank selector placard and the final two placards are for the 12 Bosch relays (two rows of six each) in the electrical bay just aft of the passenger seat.
The placards fit perfectly which made installing them a fast and simple task.”
“The electrical bay with the placards installed. It’s hard to see but just below the row of number 1 thru 6 relays is another row of 7 thru 12 relays but not all are in use right now. I wired in some extra relays and extra circuit breakers incase someone wanted to install additional electrical equipment in the future.” Continue reading
To(w) Hell & Back
Claiming that Sunday was “Tow Hell” day might be a slight exaggeration, but I wouldn’t call it a winning day either. Let’s recap the last couple days as I’ve been so busy I haven’t had time to photograph some of it.
I finally got the jeep running well on Friday after determining there was an air leak in a short piece of hose (let air in, but did not let gas out). I then timed it by ear and feel, rather than diagnostics, and that seemed to do the trick. On Saturday, I built a tow setup that utilized existing holes in the front bumper. I wanted some thing strong, but didn’t want to drill into the bumper.
Once the tow setup was ready, I turned to the exhaust. I’d already had Ann go to a muffler shop to replicate the 1.5″, 7′ section of tailpipe I needed (thankfully I had an original end section leftover from one of the DJs to use as a template). I combined the tail pipe with a Walker muffler I bought off Amazon and some Oreilly’s clamps and assembled the exhaust with relative ease.
I thought we were ready to head for Pasco on Sunday morning.

The early DJ-3As has an exhaust that pretty much was straight. The only bends needed were 1) the bend on the front piece from the manifold down to the cross member, 2) the exhaust piece has to bend over the rear axle, and 3) the exhaust bends to the outside past the gas tank (not pictured). (1955 DJ-3A manual). Good luck finding a shop that had this series of bends in their shop manuals or computer!

For comparison, this is the more likely setup that you’ll find at a muffler shop (if they have anything this old). It’s a more typical setup for 2As, 3As, 3Bs, etc. This doesn’t work for the DJ, because the muffler is positioned where the rear gas tank is installed.
We spent the first part of Sunday morning cleaning up the garage. It was a bit of a mess! Once that was done, we hooked up Patterson and began slowly towing him. We didn’t make it through the first intersection of my parent’s quiet neighborhood before I realized that the jeep wasn’t tracking around the corner. When I turned slowly right, it began to turn slowly left, forcing me to hit the brakes.
What the hell? I’ve towed a number of vehicles and never, ever run into this type of trouble.
We carefully tried a couple more corners and each was the same. The jeep began to turn the opposite way. I’d have to hop out and correct Patterson’s direction. After a trip around the block, we arrived at my parent’s house once more.
I pulled out my googler, but couldn’t find anyone having a similar problem. I concluded the drag link/ross box was somehow interfering with the jeep from tracking properly. I did read were “Dr. Verne” (aka Verne Simmons) would remove his drag link to tow it, but my custom radiator made that strategy near impossible without disassembly of multiple items. I was just about ready to remove the drag link when I decided, on a lark, to unscrew the control screw(could be the wrong name for this) on the Ross box. My assumption was that this would loosen the Ross mechanism, freeing the drag link to spin the steering wheel more easily.
My Wife’s a Genius
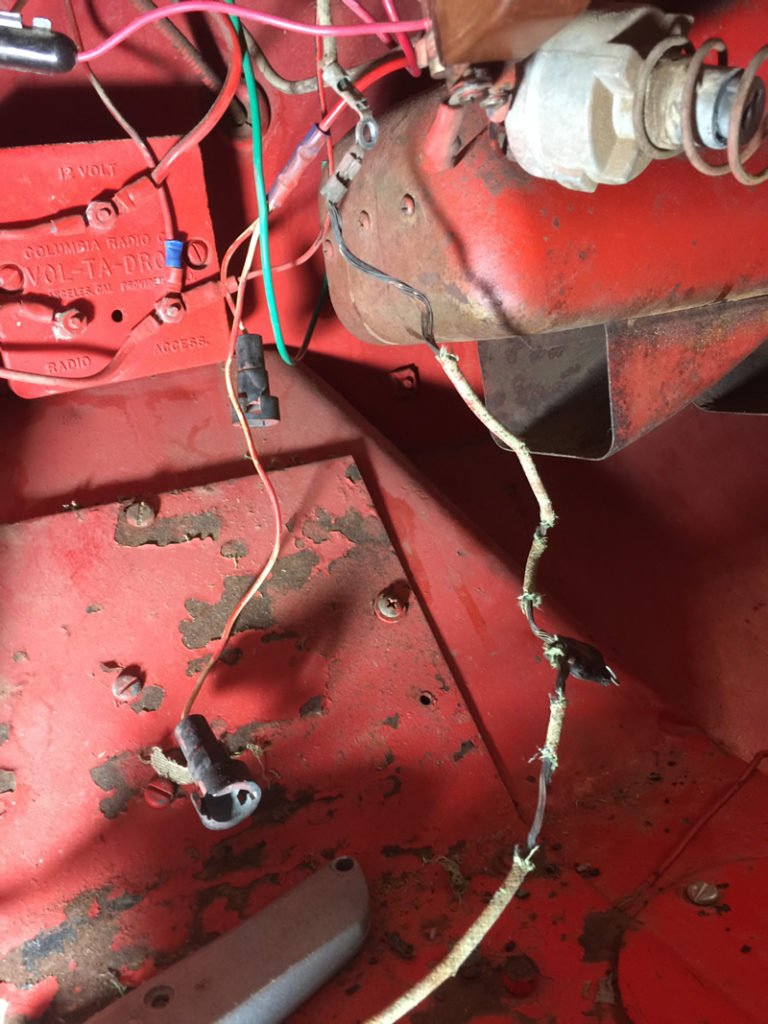
This photo provides a good look at how frayed some of the wire was behind the speedometer. Worse, this wiring was sitting on the metal brace!! in the background is the volt-a-drop which provides stepped down voltage to the King Seeley speedometer).
Electrical Mess:
We’ve been working hard on Patterson the last couple of days. Most of our time has been consumed with checking wiring and rewiring stuff. Between frayed wires and mis-wired stuff, it’s filled our time. Apart from the types of frayed wire seen in the pic above, I discovered 1) the wires to the amp gauge and light were wired into the oil light (fortunately, all I had to do was pop out the light and plug it into the amp light), 2) the amp light was missing altogether (thankfully I could steal one off of Rusty’s speedometer), 3) the ignition jumper that screws to the back of the speedometer was laying on the metal brace (must have caused some shorting), 4) the oil light wire was wired to the fuel gauge (which explains in part why the fuel gauge didn’t work … well that and there was no wire connected to the fuel tank wire.
Dimmer Switch:
The dimmer switch has been lubed, reassembled, de-painted, and installed.
The Horn Wire
Patterson came with a button attached to the side of the steering column that was used as a horn, but it didn’t work. Since we were already changing some of the wiring around, we decided to steal the column shift button wiring from Rusty’s steering column I wired last month and use it on Patterson.
To start, I knew we had to run some non-electric wire (similar to bailing wiring) through the length of the column in order to pull the horn button’s electric wire down the shaft. That sounded like a good idea, but several attempts at pushing the wire up the column were a failure: the wire kept getting snagged as I pushed it up the column. I was getting frustrated.
But then, my genius wife had an idea. Why not blow some thread down the column using an air compressor nozzle. Once the thread came out the bottom, we could pull the bailing-like wire back through. I admit, at first I thought it sounded a little crazy. After all, near the bottom of the column shaft it narrows, so I thought for sure the thread would be stopped by it. But, then I took a breath and thought …. hmmm … what could it hurt to try?
Sure enough, she produced some thread, dropped a little down the column, then stuck the air nozzle into the hole. That thread blew threw the bottom of the column in a couple seconds. It was genius! Well, almost genius, as we had to upgrade our thread to thicker thread. Other than that, we had the column horn working in no time!
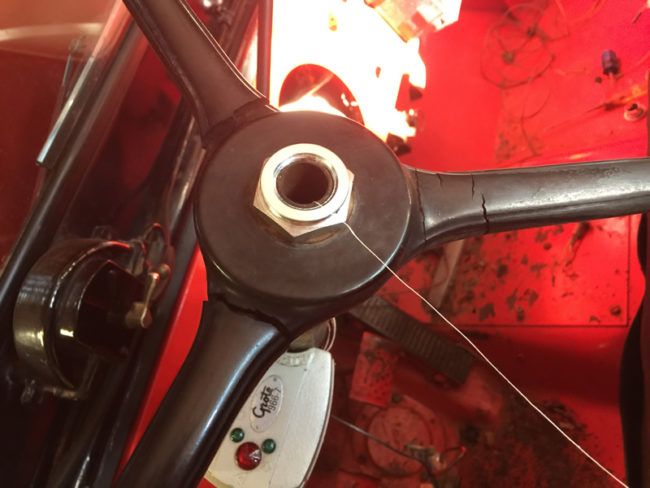
This is the thin thread we tried. It didn’t she enough tensile strength to pull up the wire. She just dropped some thread in and the air blew the rest of the thread down through that small hole at the bottom.
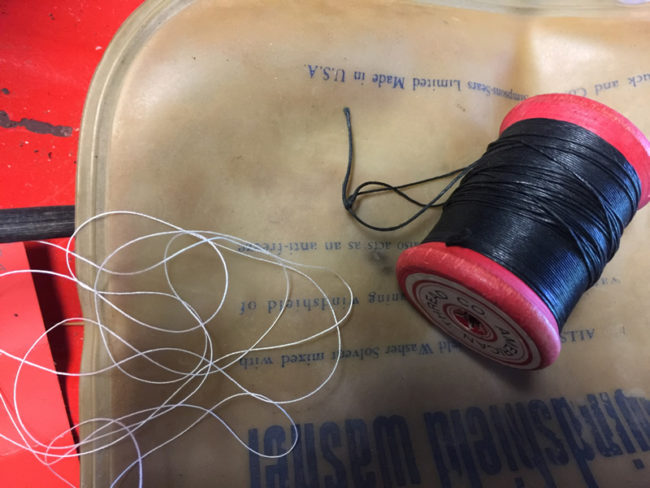
Once we shifted to the thicker, black thread it worked perfectly.
Disassembling A DJ-3A Dimmer Switch
Last week when we were in Renton, we tested Patterson’s headlights and discovered the foot-based dimmer switch wasn’t always working correctly. After a little research, I discovered the CJ-3A page had a useful thread on the topic, but naturally the switch demonstrated wasn’t exactly like the DJ-3A switch. The one shown on the CJ-3A page had a square end, while the DJ (and I’m assuming others of the same vintage?) have a rounded end. In fact, It isn’t clear to me which models use which dimmer switches?
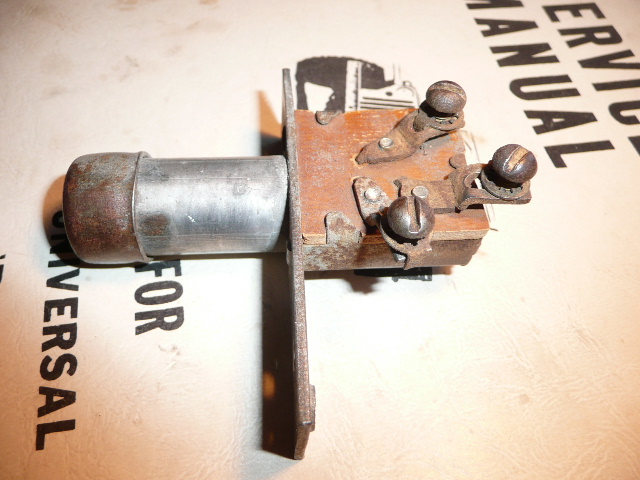
Example dimmer switch from the CJ-3A page forum.
So, here’s a look at Patterson’s switch. The first obvious difference is that the housing doesn’t have tabs. Instead, it has crimps and, let me tell you, those crimps wouldn’t bend easily outward.
Using a small screwdriver, I eventually got the crimps straightened. As soon as I tugged at the top part to remove it, everything kind of tumbled onto the table (oops).
- #1 is the bottom piece. When the actuator is depressed it catches on #1 on the bottom of the piece and spins it.
- The metal tab that sticks up on #1 connects to #2 and spins it. #2 is actually made up of 3 pieces a) the disc, b) a shaft, and c) a spring.
- #3 is a copper propeller that rotates in conjunction with #2 and #1 each time the actuator is depressed. As you can see, it is very dirty.
- Part #3 connects with copper highpoints on #4, which shifts the electricity from the high beam to the low beam, then to the high beam, etc, in a circular pattern. The contacts on #4 were dirty, too, but hard to clean without scraping the copper points. I did not have a good cleaner handy, so I only gently cleaned them.
- This is a gasket.